Mechanical Maintenance Specialist: Pumps, Compressors & Rotating Machinery
Tickets
Mechanical Maintenance Specialist: Pumps, Compressors & Rotating Machinery
Mechanical Maintenance Specialist: Pumps, Compressors & Rotating Machinery
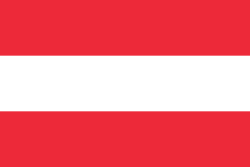
Introduction:
Rotating machinery, including pumps and compressors, is critical to the operation of industrial facilities. Mastering the maintenance of such equipment ensures reliability, reduces downtime, and extends asset life , to meet this essential need Seattle International Institute for Training offers a specialized training course aimed at developing advanced skills in the maintenance, troubleshooting, and optimization of pumps, compressors, and other rotating machinery.
This course blends theoretical knowledge with practical techniques, preparing participants to handle complex maintenance challenges with confidence.
Objectives:
Participants in this course will learn to:
Ø Understand the principles of operation for pumps, compressors, and rotating equipment.
Ø Master maintenance strategies for improving equipment performance.
Ø Develop troubleshooting skills for mechanical failures.
Ø Learn best practices for alignment, balancing, and vibration control.
Ø Strengthen the ability to implement preventive and predictive maintenance programs.
Target Audience:
This course is ideal for:
Ø Mechanical maintenance engineers and technicians.
Ø Plant maintenance supervisors and managers.
Ø Reliability engineers and asset management specialists.
Ø Operations engineers responsible for equipment upkeep.
Ø Anyone involved in maintaining or managing rotating machinery.
Course Outline:
Day 1: Fundamentals of Rotating Machinery
- Introduction to rotating equipment types and applications.
- Operational principles of pumps and compressors.
- Key performance parameters and system integration.
- Safety practices in handling rotating machinery.
- Understanding wear, fatigue, and operational stresses.
Day 2: Maintenance of Pumps
- Overview of pump classifications and applications.
- Inspection and maintenance techniques for pumps.
- Diagnosing pump failures: cavitation, seal failures, misalignment.
- Preventive maintenance practices.
- Pump performance testing and analysis.
Day 3: Maintenance of Compressors
- Compressor types: reciprocating, centrifugal, rotary screw.
- Compressor maintenance routines and inspection.
- Common compressor problems and troubleshooting.
- Efficiency improvements and maintenance optimization.
- Case study: Compressor failure investigation.
Day 4: Vibration Analysis and Equipment Reliability
- Basics of vibration analysis for rotating machinery.
- Alignment and balancing techniques.
- Identifying vibration causes and remedies.
- Reliability-centered maintenance (RCM) concepts.
- Using predictive maintenance tools effectively.
Day 5: Advanced Troubleshooting and Best Practices
- Structured troubleshooting approaches.
- Root cause failure analysis (RCFA).
- Spare parts management and inventory control.
- Continuous improvement strategies in maintenance.
- Final workshop: Developing a maintenance plan for rotating machinery.
Tickets
Related Cources
Petroleum Economist: Petroleum Economics & Cost Management
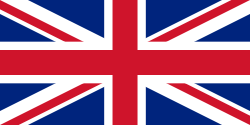
SECURITY MANAGEMENT, PLANNING & ASSET PROTECTION WITH INTEGRATED SECURITY SOLUTIONS
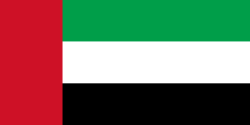
Flare Gas Recovery & Emission Control
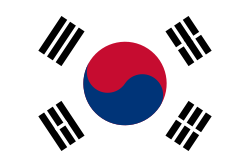
Flare Gas Recovery & Emission Control
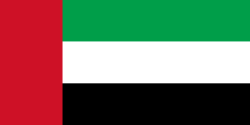
Advanced LNG Vaporization & Cold Energy Recovery
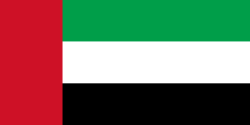
Advanced LNG Vaporization & Cold Energy Recovery
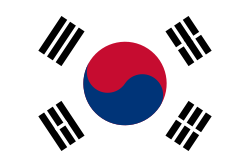
Advanced Oilfield Production Chemistry & Flow Assurance
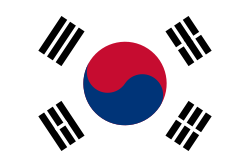
Advanced Oilfield Production Chemistry & Flow Assurance
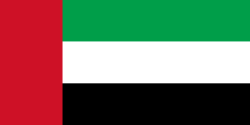
Advanced Artificial Lift Systems: Design & Troubleshooting
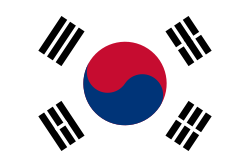
Advanced Artificial Lift Systems: Design & Troubleshooting
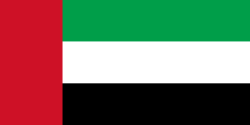