Maintenance Strategy Development and Cost Effective Implementation
Tickets
Registrations are closed
Maintenance Strategy Development and Cost Effective Implementation
Maintenance Strategy Development and Cost Effective Implementation
19 -
23
Jan
2025
Istanbul,
Turkey
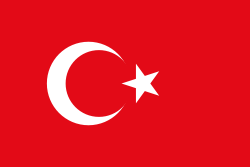
What are the Goals?
By the end of this Maintenance Strategy Development and Cost Effective Implementation training course, delegates will be able to:
- Understand the concepts of costs, capital, profit and ROI
- Understand the cost impact of unanticipated failure
- Apply proactive policies to reduce future maintenance costs
- Structure and analyse failure data to reduce repetitive failures
- Identify root causes of unanticipated failure costs
- Reduce resource costs through efficient work management practices
- Decide rationally what maintenance activities to outsource and what not
- Use the features, functions and benefits of lean maintenance contracts
- Use the most applicable type of maintenance contracts (incl. Service Level Agreements) and when/how to apply them
- Define service levels and monitor the contractor performance
- Develop and negotiate a maintenance contract
- Recognize the pitfalls
- Evaluate the delivered performance of all parties involved
- Implement maintenance contract management
Who is this Training Course for?
This Maintenance Strategy Development and Cost Effective Implementation training course is suitable to a wide range of professionals, but will greatly benefit:
- Planners
- Supervisors
- Engineers
- Reliability engineers
- Maintenance team leaders and managers
- Operations team leaders and managers
- All professionals involved in procurement and supply chain management
- All professionals negotiating, managing and verifying maintenance contracts
- Teams who have been assigned the responsibility of establishing a maintenance contract will find it extremely useful to attend this course as a unit
- Anyone who wishes to update themselves on Maintenance Contracts & Outsourcing
Daily Agenda
Equipment Life-cycle Cost Introduction
- Definitions of reliability, maintenance & asset management
- The concept of costs, capital, profits and return on investment
- The ‘Asset Healthcare Model’
- Key areas of asset management
- Open discussion sessions
Cost Factors and Causes
- The real cost of unanticipated failure
- Asset performance standards
- The forms of asset failure and degradation
- The causes and nature of asset failure and degradation
- The effects, cost and risks of asset degradation
Breaking the Cycle of Degradation and Costs
- Programmed maintenance
- Programmed maintenance intervals
- Condition-based maintenance intervals
- Implementing optimised PM programs
- Optimizing spares to support the maintenance program
Cost Reduction through Defect Elimination
- Failure data collection and analysis
- The impact of chronic failures versus intermittent failures
- Focus improvement through Pareto analysis
- Quantify losses in life cycle terms
- Rigorous root cause analysis techniques
- Discussion of software and templates to support analysis
Work Management converts Strategy to Practice
- Work identification and defect reporting
- The importance of backlog
- Planning for quality and reliability
- Capacity planning
- Scheduling for efficiency
- Work logistics and preparation
- Checklists and practical aspects work quality control
- Final discussion and evaluation
Outsourcing Considerations
- Introduction
- Asset management - The business impact of maintenance
- Considerations in outsourcing maintenance – what to outsource and what not?
- Risks involved
Maintenance Contracts
- Maintenance contract types
- Parties involved
- The tendering process – modern ways of tendering
- Choosing the right contractor
- Costing the service
- Defining Key Performance Indicators to monitor the performance of all parties involved
- Use of Balanced Scorecard with performance contracts
Developing the Maintenance Contract
- Vendor management
- The contracting cycle
- Assemble a team
- Assess, determine and specify the required service levels
- Writing the contract – contents of a maintenance contract
- Implementing contract management – how to make it work (performance management)
- Periodic evaluation & improvement
Grounding and Negotiating the Contract
- Expectations about availability, reliability and costs
- The extensive preventive maintenance schedule – “tricks” of maintenance contractors
- The seven steps to develop a risk based maintenance concept
- Using the maintenance concept to negotiate more effectively lean maintenance contracts
- Negotiating the contract – negotiation ploys
- Negotiating the contract – negotiation tactics
- Negotiating tips
Final Workshop
- Development of a maintenance contract in groups
- Defining the requirements and service levels
- Develop the offer
- Selection criteria
- Presenting the bid
- Closing the contract
- Evaluation of results
- Wrap-up
Tickets
Registrations are closed