API 570 : Piping Inspection Code (API Exam Preparation Training)
Tickets
Registrations are closed
API 570 : Piping Inspection Code (API Exam Preparation Training)
API 570 : Piping Inspection Code (API Exam Preparation Training)
01 -
05
Dec
2024
Kuala Lumpur,
Malaysia
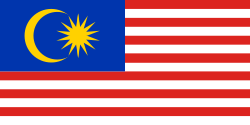
What are the Goals?
At the end of this API 570 training course, you will learn to:
- how to use the tables in the process piping codes ASME B31.3
- Understand the procedure for measuring the corrosion rate LT&ST for the piping systems and circuits
- Calculate the remaining life and MAWP
- Acquire knowledge about common damage mechanisms in piping inside the refinery
- Obtain data about welding processes, qualifications and metallurgy
- Use the proper NDE technique during in-service inspection
- Know how to read the relative inspection plans
Who is this Training Course for?
This training course is suitable to a wide range of professionals but will greatly benefit:
- Piping Inspectors
- NDE Examiners
- Piping Inspection Engineers
- Plant Inspectors
- Piping Engineers
- Mechanical Engineers
- Corrosion Engineers
Daily Agenda
Day One : API RP 577, ASME BPVC Section V and ASME IX
- Getting Started - Exam & Study Tips
- API RP 577, Welding Processes, Inspection, and Metallurgy
- ASME Section V, Non-destructive Examinations, Articles 1, 2, 6, 7, 9, 10, and 23 (Section SE-797 only)
- The weld procedure review:
- Weld Procedure Specification (WPS)
- Procedure Qualification Record (PQR)
- Welder Performance Qualification (WPQ)
- Essential and non-essential variables have been properly addressed.
- Number and type of mechanical tests listed on PQR.
Day Two : ASME B16.5, API 578 & API 576
- Flanges Pressure Temperature Ratings
- Flanges Markings
- Flanges Materials
- Flanges Dimensions
- Flanges Test
- Material Verification Program for New and Existing Assets API 578
- Case studies on failed Materials due to lack of MVP.
- API 576 - Sections 5
- API 576 - Sections 6.1-6.3
- API 576 - Section 8
- API 576 - Sections 10.1-10.3
Day Three: ASME B31.3
- Scope and code limitations
- Casting Quality factor, Ec from ASME B31.3, 302.3.3(b) and Table A-1A
- Weld Joint Quality factors from ASME B31.3, 302.3.4 and Table A-1B;
- Increased Joint Quality Factors by performing supplemental NDE
- The minimum required thickness or pressure design thickness of a straight pipe section for internal pressure only
- The minimum required thickness of a permanent blank for a given design pressure
- The "MAWP" of corroded pipe, compensating for expected corrosion loss at the next inspection.
- Thermal expansion of a material between temperatures.
- The minimum metal temperature of a material, which is exempt from impact testing
- Determination of the minimum required Charpy V-notch impact values of a given material.
- Weld sizes require preheating and/or heat treatment.
- Mandatory preheat and PWHT tables
- NDE and Inspection requirements
- Hydrostatic leak testing Requirements
- Pneumatic leak testing Requirements
- Calculation of a hydrostatic or pneumatic leak test pressure
Day Four: API 570
- Scope
- Terms, Definitions, Acronyms, and Abbreviations
- Owner/User Inspection Organization
- Inspection, Examination, and Pressure Testing Practices
- Interval/Frequency and Extent of Inspection
- Inspection Data Evaluation, Analysis, and Recording
- Repairs, Alterations, and Rerating of Piping Systems
- Annex A, C & D
- Solved problems (LT&ST Corrosion rate)
- Solved problems (MAWP)
- Solved problems (Remaining life)
Day Five: API RP 571, API RP 547 & ASME PCC-2
- Amine Stress Corrosion Cracking
- Atmospheric Corrosion
- Boiler Water and Stream Condensate Corrosion
- Caustic Corrosion
- Caustic Stress Corrosion Cracking
- Chloride Stress Corrosion Cracking
- Corrosion Under Insulation
- Erosion/Erosion – Corrosion
- Galvanic Corrosion
- Hydrochloric Acid Corrosion
- Mechanical Fatigue (Including Vibration-induced Fatigue)
- Microbiologically Influenced Corrosion
- Soil Corrosion
- Sour Water Corrosion (Acidic)
- Sulfidation
- Inspection Practices for Piping System Components API 574
- API 574 Tables
- ASME PCC-2 - Article 101: Scope, Organization, and Intent
- ASME PCC-2 - Article 201: Butt-Welded Insert Plates in Pressure Components
- ASME PCC-2 - Article 206: Full Encirclement Steel Reinforcing Sleeves for Piping
- ASME PCC-2 - Article 209: Alternatives to Post weld Heat Treatment
- Article 210: In-Service Welding on to Carbon Steel Pressure Components or Pipelines
- Article 211: Weld Buildup, Weld Overlay, and Clad Restoration
- Article 212: Fillet Welded Patches
- Article 304: Flaw Excavation and Weld Repair
- Article 305: Flange Repair and Conversion
- Article 306: Mechanical Clamp Repair
- Article 501: Pressure and Tightness of Piping and Equipment
- Article 502: Non-destructive Examination in Lieu of Pressure Testing for Repairs and Alternations
Tickets
Registrations are closed